6548, Из истории металлургии железа Послано Reader, 03-10-2008 13:40
Коснусь кратко истории получения железа и конструкции печей, не затрагивая вопросы термической обработки.
Источники http://lon-live-metal.narod.ru/Revolution_2_Me.htm http://roskuz.ucoz.ru/publ/2-1-0-4 Упоминания о древних греках, римлянах и китайцах выбросил. Курсив далее мой.
С древнейших времен ковкое губчатое железо получали путем «прямого восстановления» непосредственно из руды. В XVIII в. этот так называемый сыродутный процесс был широко распространен. В Европе он сохранился вплоть до 1850г., а в Северной Америке—даже до 1890г.
В наше время сыродутные (кричные) горны еще можно встретить у народов Центральной Африки и в Китае.
Прогрессивные китайцы, которые изобрели все на свете тысячи лет назад, в том числе и переделку чугуна в сталь, до 20 века пользовались сыродутными печами.
Поначалу этот металл представлял собой ковкое железо, или очень мягкую сталь (пока для простоты мы будем называть сталью сплав железа с малым количеством углерода). Были известны и более твердые сорта стали, однако способы их получения кузнецы держали под строжайшим секретом.
Слово «Мягкая» сталь и железо не должны вводить в заблуждение, будто они ни к чему не пригодны. Для примера можно вспомнить «мягкую» строительную арматуру или гвозди (Ст3, закалке не подвергается, содержание углерода 0,14 - 0,22%). Из такой стали вполне можно делать мечи, ножи, копья, доспехи и они будут лучше бронзовых. Процесс ковки, за счет наклёпа, улучшает свойства стали, даже без термической обработки (вспомним, как отбывают косы).
На первых порах свойства получаемого продукта людей вполне устраивали. И задача стояла получить как можно больше железа. Проблема была не столько в качестве, сколько в количестве. Ведь не даром же оно ценилось вначале даже больше золота.
Получив полезный продукт в сыродутной печи, человек, чтобы получить еще больше железа, наверняка сразу стал совершенствовать эту печь путем ее увеличения. Не может быть, чтобы люди на протяжении тысяч лет изготавливали железо в маленьких сыродутных печах не пытаясь их увеличить.
Поэтому между первым получением железа в малой сыродутной печи и производством его в больших шахтных печах не может быть большого временного промежутка в тысячелетия.
А секрет состоял прежде всего в повышении содержания углерода: такая сталь приобретает способность к закалке.
С увеличением размеров сыродутных горнов и интенсификацией труда возрастало и содержание углерода в железе.
При этом температура плавления железа оказывалась ниже и часть его вытекала из горна в расплавленном виде вместе со шлаком.
Таким образом, металлурги стали получать побочный продукт, который в твердом состоянии хрупок и легко разбивается молотом.
Это был ЧУГУН.
Вначале его просто выбрасывали, но потом научились использовать
Бытует заблуждение, что для получения чугуна нужно обязательно достичь температуры плавления железа 1538 °C, и для этого обязательно необходим каменноугольный кокс. Это не верно. Для получения чугуна теоретически достаточно 1200°C. В той же сыродутной печи, происходит не только восстановление железа из оксидов, но и его науглероживание через газовую фазу. С увеличением содержания углерода в железе температура плавления падает и при достаточно больших размерах печи появляется жидкая фаза – чугун.
( В присутствии окиси углерода губчатое металлическое железо постепенно науглероживается по реакции:
3Fe + 2CO = Fe3C + CO2 (8)
Температура его плавления понижается вплоть до 1150…1200°C. Вследствие этого науглероженное железо (от 1,8 до 2 % C) переходит в жидкое состояние (расплавляется) и стекает по каплям между кусками раскалённого кокса на лещадь горна доменной печи. Во время перемещения капелек металла происходит дополнительное насыщение железа углеродом примерно до 3,5…4 %, т.е. до обычного содержания углерода в жидком чугуне. http://etelien.ru/Collection/38/38_00028.htm )
СЫРОДУТНАЯ ПЕЧЬ
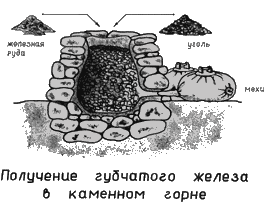
В земле выкапывалась яма, в которую закладывались руда и уголь, над ямой сооружался купол с короткой трубой, а с боку прилаживался мех для дутья. Когда процесс заканчивался, печь разрушали и доставали крицу.
Одна печь выдавала крицу весом в среднем около 3 кг, на треть состоящую из железа. Но при проковке крицы много железа снова окислялось или оставалось в шлаке. Процесс был фантастически непроизводительным, особенно если вместо руды использовался красный песок или болотная грязь.
Даже из самой легкоплавкой руды в сыродутной печи восстанавливалось не более половины железа. В общем, можно считать, что сыродутная печь давала в среднем не более 500 граммов железа.
Когда впервые получили железо в сыродутной печи, мы, наверное, не узнаем, но как я уже говорил, это произошло, вряд ли задолго до первых шахтных печей.
В средние века горн уже обрел вид шахтной печи, достигавшей в высоту нескольких метров. Теперь печи «дышали» с помощью энергии воды- воздуходувные мехи приводились в движение сначала специальными водяными трубами, а позже огромными водяными колесами.
Более высокую ступень в развитии чёрной металлургии представляли собой постоянные высокие печи называемые в Европе штукофенами. Это действительно была высокая печь, — с четырёхметровой трубой для усиления тяги. Мехи штукофена качались уже несколькими людьми, а иногда и водяным двигателем. Штукофен имел дверцы, через которые раз в сутки извлекалась крица.
В конце XIII века штукофены стали появляться в Германии и Чехии (а ещё до того были на юге Испании) и в течение следующего века распространились по всей Европе. Производительность штукофена была несравненно выше, чем сыродутной печи, — в день он давал до 250 кг железа, а температура плавления в нем оказывалась достаточна для науглероживания части железа до состояния чугуна. Однако штукофенный чугун при остановке печи застывал на её дне, смешиваясь со шлаками, а очищать металл от шлаков умели тогда только ковкой, но как раз ей-то чугун и не поддавался. Его приходилось выбрасывать. Иногда, впрочем, штукофенному чугуну пытались найти какое-то применение. Например, древние индусы отливали из грязного чугуна гробы, а турки в начале XIX века — пушечные ядра.
Металлурги давно заметили связь между температурой плавления и выходом продукта, — чем выше она была, тем большую часть содержащегося в руде железа удавалось восстановить. Потому, рано или поздно им приходила мысль форсировать штукофен предварительным подогревом воздуха и увеличением высоты трубы. В середине XV века в Европе появились печи нового типа, — блауофены, которые сразу преподнесли сталеварам неприятный сюрприз. Более высокая температура плавления действительно значительно повысила выход железа из руды, но она же повысила и долю железа науглероживающегося до состояния чугуна. Теперь уже не 10%, как в штукофене, а 30% выхода составлял чугун, — «свиное железо» ни к какому делу не годное. В итоге, выигрыш часто не окупал модернизации. Блауофенный чугун, как и штукофенный, застывал на дне печи, смешиваясь со шлаками. Он выходил несколько лучшим, так как его самого было больше, следовательно, относительное содержание шлаков выходило меньше, но продолжал оставаться малопригодным для литья. Чугун получаемый из блауофенов оказывался уже достаточно прочен, но оставался ещё очень неоднородным, — из него выходили только предметы простые и грубые, — кувалды, наковальни. Уже прилично выходили пушечные ядра. Кроме того, если в сыродутных печах могло быть получено только железо, которое потом науглероживалось, то в штукофенах и блауофенах внешние слои крицы оказывались состоящими из стали. В блауофенных крицах стали было даже больше, чем железа. С одной стороны, это казалось хорошо, но, вот, разделить-то сталь и железо оказывалось весьма затруднительно. Содержание углерода становилось трудно контролировать. Только долгой ковкой можно было добиться однородности его распределения.
экспериментируя с чугуном, скоро открыли передельный процесс, поднимающий металлургию железа на качественно новый уровень.
Передельный процесс в металлургии получил распространение в Европе с 16 века. Следующим этапом в развитии металлургии стало появление доменных печей. За счёт увеличения размера, предварительного подогрева воздуха и механического дутья, в такой печи все железо из руды превращалось в чугун, который расплавлялся и периодически выпускался наружу. Производство стало непрерывным, — печь работала круглосуточно и не остывала. За день она выдавала до полутора тонн чугуна.
Чтобы приготовить из чугуна ковкое железо, необходимо удалить из него углерод, т. е. подвергнуть его дальнейшей обработке, которая у металлургов получила название «кричный передел»
Открытие и освоение такого способа обработки позволило постепенно перейти от кричных сыродутных горнов к рудоплавильным печам—домницам.
В них стали получать жидкий чугун, который затем превращали в мягкое железо,а позднее—в сталь(удаляя избыточный углерод).
Так возник двухступенчатый—через промежуточный продукт (чугун)—способ производства стали.
Это типичный пример того, как простое увеличение размеров оборудования, в данном случае сыродутных горнов, может привести к принципиально новой технологии. Вместе с ростом потребности в ковком железе и стали постоянно возрастал спрос и на древесный уголь, однако в богатых рудой районах леса были вырублены.
Особенно заметно это было в Англии.
Но шахтные печи для выплавки чугуна (теперь их называют домнами), как и печи для дальнейшего его передела, нуждались в древесном угле.
В 1709 г. Абрахаму Дерби из английского города Колбрукдейл впервые удалось применить в доменной печи каменноугольный кокс и тем самым модернизировать первую ступень процесса производства стали. (По другим сведениям это произошло в 1735 году)
Однако для переработки чугуна в сталь по-прежнему был необходим древесный уголь.
Каменный уголь тогда еще не умели использовать для этой цели: содержащаяся в нем сера переходила в сталь, делая ее непригодной.
Проблему решил англичанин Генри Корт в 1784 г. Изобретенный им способ пудлингования (от английского рuddlе-месить, перемешивать) означал новый большой шаг вперед, и это по праву можно считать началом современной металлургии стали.

В пудлинговой печи топливо уже не соприкасается с чугуном, подлежащим переработке.
Каменный уголь сгорает в топке, которая отделена от горна порогом.
Первые пудлинговые печи имели две дымовые трубы: одну непосредственно над топкой, другую с противоположного конца печи, над плавильным горном, или ванной.
Пудлингование—это очистка чугуна в пламенной печи.
Процесс начинается с загрузки чугуна в горн. Чтобы ускорить плавку, куски чугуна весом 10—30 кг (всего обрабатывается около 150 кг) помещают вблизи порога топки, где температура самая высокая.
Примерно через 45 мин чугун расплавляется.
Пудлинговщик вставляет в загрузочное окно печи железную штангу с крюком на конце и проводит ею борозды по тестообразной чугунной массе (массу металла, расплавленного в печи, металлурги называют ванной).
При этом чугун хорошо перемешивается и поверхность ванны увеличивается. Закрывая горн и забрасывая влажный шлак, пудлинговщик регулирует температуру ванны.
Кроме того, в ванну добавляют песок, который, вступая в химическую реакцию с футеровкой печи, образует шлак; последний окисляет углерод в чугуне. В период кипения ванна сильно бурлит за счет окисления углерода, и чем больше его окисляется, тем сильнее разжижается ванна, и железные зерна собираются там в комья.
Пудлинговщик ломом много раз переворачивает массу и наконец разделяет ее на три-пять частей—криц.
Они еще горячими попадают к кузнецу, который к каждой крице приваривает железный стержень дюймовой толщины и проковывает их в «колбаски» диаметром 7—10 см и длиной около 50 см.
Эти заготовки в прокатной машине раскатывают в полосы, затем снова разделяют на куски длиной 50 см и еще раз прокатывают, накладывая по 4 полосы одна на другую. Для процесса пудлингования были характерны именно эти операции прокатки криц, которые требовались не столько для придания заготовке формы, сколько для того, чтобы сварить зерна и комки железа. В результате получалось так называемое сварочное железо (или сварочная сталь).
Одна пудлинговая печь за сутки давала 3500 кг крупнозернистого кричного железа либо 1600 кг мелкозернистого железа— пудлинговой стали.
Пудлингование означало существенный прогресс по сравнению с прежним сыродутным способом и кричным переделом.
Во-первых, вместо дефицитного древесного угля теперь можно было обходиться каменным углем.
Во-вторых, пудлинговые печи оказались намного производительнее. И наконец, в результате пудлингования получали сварочное железо (или сварочную сталь)—материал с отличными свойствами.
Однако сварочное железо и сварочная сталь имели и серьезный недостаток—неравномерность состава по поперечному сечению.
Английский часовщик Бенджамин Хантсмен (1704—1776) пришел к мысли, что состав этих материалов можно выровнять путем переплавки.
Эта идея была не нова, и раньше не раз пытались таким путем улучшить однородность и качество сварочной стали, но безуспешно.
Чтобы получить жидкую сталь, Хантсмен использовал тигель из огнеупорного материала и обогреваемую коксом печь с дутьем и высоким горном. Это принесло успех. Французские кузнецы первыми изготовили из литой стали, твердой и потому труднее поддающейся ковке, ножи, которые оказались лучше шеффилдских.
Высококачественная тигельная сталь обладала превосходными свойствами в литом состоянии. Спустя столетие после изобретения Хантсмена из нее стали делать паровозные оси, а еще позже - орудийные стволы.
В 1851 г, на Лондонской всемирной выставке был показан стальной слиток весом 2150 кг. Чтобы получить такую большую отливку, пришлось сливать в миксер (копильник) расплавленную сталь из многих тиглей емкостью по 45 кг каждый.
В эпоху промышленной революции потребность в железе настолько сильно возросла, что ее не мог удовлетворить и пудлинговый процесс. К тому же различные новые технические применения пудлингового железа показали, что оно не выдерживает больших нагрузок. Например, так как железнодорожные локомотивы становились тяжелее и быстроходнее, рельсы, изготовленные из пудлинговой стали, все чаще ломались. Основателем сталеплавильного производства следует считать Генри Бессемера (1813—1898).
В 1885 г. он впервые получил ковкое железо, вернее сталь, путем продувки воздухом 5 кг сырого чугуна, расплавленного в тигле из огнеупорной глины.


Оказалось, что при продувке воздухом расплавленный чугун не только не охлаждается, как предполагали прежде, но, напротив, его температура возрастает настолько, что ванна остается жидкой, хотя сталь, которая образуется из чугуна благодаря продувке, имеет более высокую температуру плавления. 17 октября 1855 г. Бессемер получил английский патент на свое изобретение.
Новый процесс получения стали из чугуна «без топлива и без топки» прошел длинный, усеянный множеством неудач путь, прежде чем стало ясно, что хорошую сталь дает только малофосфористый чугун. Если же в чугуне много фосфора, то продукт получается хуже, чем ковкое железо,—он оказывается пористым «красноломким» и «холодноломким» (т.е. хрупким в горячем и в холодном состояниях).
Вследствие этих сложностей бессемеровский процесс распространялся весьма медленно—сначала он был принят в Швеции, затем—в Австрии и только позднее—в Англии. Широкому его распространению препятствовало то, что он нуждался в малофосфористом чугуне. В результате главной проблемой стала очистка чугуна от фосфора.
Среди многих металлургов, которые пытались решить эту проблему, первым достиг успеха Сидней Джилкрист Томас (1850-1885). Томас имел две специальности. Он служил писарем в лондонском полицейском суде, чем зарабатывал на жизнь, и одновременно изучал химию и металлургию в Горном училище, где и заинтересовался проблемой удаления фосфора из чугуна. В 1877 г. Томас подал первую заявку (а в 1878—1879 гг.—еще две) на способ получения стали, который позднее был назван его именем.
Непосвященный не увидит особой разницы между бессемеровским и томасовским процессами.
В основе обоих процессов лежит один и тот же принцип: чугун, из которого получают сталь, очищают, продувая через него воздух.
Сосуд, где протекает реакция,— конвертер —имеет грушевидную форму с открытой горловиной вверху; он укреплен на горизонтальной оси, что позволяет его наклонять. Конвертеры Бессемера и Томаса по внешнему виду одинаковы. Главное различие заключается в том, что бессемеровский конвертер изнутри выложен - кислой (т. е. кислотной по своему химическому характеру) огнеупорной футеровкой и в нем нельзя удалить фосфор из богатого им чугуна в основной шлак (т. е. по своим химическим свойствам подобный основаниям), потому что такой шлак быстро разъедает кислую футеровку. Томасовский же конвертер имеет основную футеровку, поэтому здесь, добавляя известь, можно получить основной шлак, который хорошо извлекает фосфор из чугуна, но не разрушает основную футеровку.
Конвертер —будь то бессемеровский или томасовский—позволяет за 20 мин превратить в сталь до 20 т чугуна. Для производства такого же количества стали в горне способом кричного передела потребовалось бы три недели, а в пудлинговой печи—неделя.
Так металлурги получили в свое распоряжение два высокопроизводительных процесса, что позволило удовлетворять непрерывно возрастающий в промышленных странах спрос на сталь. Бессемеровский и томасовский конвертеры были необходимы для массового производства стали общего назначения, тогда как высококачественные специальные стали продолжали выплавлять в тиглях.
Но техника не стояла на месте.
Братья Вильгельм и Фридрих Сименсы изобрели регенеративный способ обогрева печей и, после того как Фридрих Сименс получил патент на это изобретение, построили опытную печь. Основная идея регенеративного обогрева заключается в предварительном подогреве воздуха, необходимого для горения топлива, отходящими газами-продуктами горения. Для этого через определенные промежутки времени воздух направляют то через один, то через другой регенератор (пока воздух для горения, проходя через один регенератор и охлаждая его, сам нагревается, отходящие газы подогревают другой регенератор).
В опытной печи братьев Сименсов стальные напильники через 6 ч расплавились, а тигель, помещенный в топочную камеру, превратился в шлак. Первые практические попытки выплавить тигельную сталь в подобной печи на сталелитейном заводе в Шеффилде закончились неудачей.
Вместе со сталью плавились тигель и стенки печи.
8 апреля 1864 г. на одном из заводов Южной Франции Пьеру Мартену (1824—1915) впервые удалось сварить хорошую сталь в регенеративной печи, построенной при участии Вильгельма Сименса. Шихта (загружаемые в печь исходные материалы) состояла из чугуна, выплавленного из гематита—красного железняка с острова Эльба, чушек пудлингового железа и стального лома.
Мартеновский процесс (немцы его называют сименс-мартеновским) наряду с бессемеровским и томасовским ознаменовал еще один важный шаг в развитии сталелитейного производства1. Этот процесс сохранил большое практическое значение до наших дней; особенно широко он используется для повторного производства стали из лома и стальных отходов (как говорят металлурги, из «скрапа»).
Новый процесс получил широкую известность после Парижской выставки 1867 г.
В России первую мартеновскую печь построили в 1869—1870гг. на Сормовском заводе А.А.Износков и Н.Н. Кузнецов.
Наконец мир избавился от «стального голода».
Получив в свое распоряжение такие высокопроизводительные технологические процессы, Англия благодаря изобретениям Бессемера и Сименса упрочила свое положение ведущей промышленной державы.
Уже в 1870 г. производство стали в Англии превысило 5 млн. т и продолжало быстро расти.
Таким образом, за столетие был достигнут примерно стократный прирост: во второй половине XVIII в. в Англии производилось за год порядка 50—100 тыс. т стали.
Таким образом технологические революции в металлургии:
Домны и передел чугуна 16 век (по ТИ).
Использование каменноугольного кокса, который позволяет снять дефицит древесного угля 18 век
Первая плавка стали в тигле небольшого объёма конец 18 века
Сталеплавильное промышленное производство (конвертор, мартен) конец 19 века.
|